Empresas brasileiras se adaptam à indústria 4.0
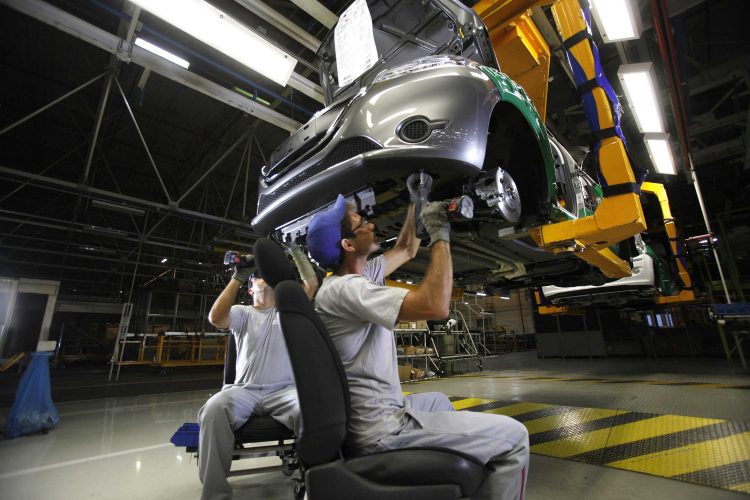
Passada a fase mais crítica da crise econômica, empresas começam a pôr em prática planos para se adaptarem à chamada indústria 4.0. Na visão de executivos, analistas e do governo, 2018 será um ano de importante avanço de projetos para o País não ficar à margem do que é considerado a quarta revolução industrial.
A expectativa é que, em dez anos, 15% das indústrias atuem no conceito da indústria 4.0, que se dá principalmente pela digitalização e robotização. Hoje, menos de 2% das empresas estão inseridas nesse conceito, segundo a Agência Brasileira de Desenvolvimento Industrial (ABDI), ligada ao Ministério da Indústria e Comércio (MDIC).
Esse porcentual já é realidade na Alemanha, na Coreia do Sul, nos EUA e em Israel, e cresce anualmente. “Felizmente, 2018 vai marcar a arrancada da indústria brasileira para a transformação digital”, diz José Rizzo, presidente da empresa de automação Pollux e da Associação Brasileira de Internet Industrial (ABII)
A Pollux, que em 2017 registrou crescimento de 93% nos negócios, iniciou o ano com aumento significativo de pedidos de orçamentos de empresas que querem iniciar processos de digitalização para melhorar a produtividade e a competitividade. Segundo Rizzo, o custo do processo é mais viável hoje.
Ele cita que o preço médio de sensores baixou 66% de 2004 até agora, de US$ 1,30 para US$ 0,44, e deve chegar a US$ 0,38 em 2020. O custo do armazenamento de dados deve cair 80%.
Uma das maiores empresas na área de tecnologia e automação, a ABB espera alta de mais de 5% na demanda por serviços e produtos
“Muitas empresas estão fazendo planos efetivos de automação, digitalização e introdução da indústria 4.0”, diz Rafael Paniagua, presidente da ABB. Entre os setores mais avançados estão mineração, papel e celulose, químico, alimentos, bebidas e eletrônicos.
A sócia para a área de tecnologia da Deloitte, Márcia Ogawa, diz que a consultoria tem atendido, em média, dez empresas por mês com encomendas de planos para adotar a manufatura 4.0. “Dada a concorrência internacional, o Brasil precisa correr para se atualizar e fazer parte do novo ecossistema global.”
Para Márcia, o temor da perda de empregos com o uso mais intenso de tecnologias avançadas não pode travar a inovação. “Se fosse assim, ainda estaríamos usando charretes.” Ela ressalta que a mão de obra precisa se requalificar e se adaptar, como ocorreu em outros momentos de rupturas tecnológicas.
Na unidade de autopeças da ThyssenKrupp em Poços de Caldas (MG), inaugurada há dois anos, todo o processo produtivo segue o conceito de fábrica inteligente. O diretor Roberval Calca diz que a produtividade é elevada e o índice de refugo é baixo. A unidade produz 700 mil módulos ao ano com 72 funcionários. “Se fosse uma fábrica convencional seriam necessários 200 trabalhadores.”
Política nacional
O presidente da ABDI, Guto Ferreira, informa que a entidade vai lançar, em março, a Política Nacional da Indústria 4.0 com diretrizes para a transformação digital, durante o Fórum Econômico Mundial, em São Paulo.
“Vamos mostrar quais serão os primeiros setores a serem apoiados pelo governo”, avisa Ferreira. “Não tem incentivo fiscal, mas apoio como linhas de financiamento.” Cálculos da ABDI indicam que a adoção de conceitos da indústria 4.0 podem gerar economia anual de R$ 73 bilhões para o setor produtivo com a redução de custos.
A Vale economizou no ano passado US$ 50,5 milhões em ações como digitalização de processos e inteligência artificial. “Neste ano, a meta é somar US$ 100 milhões em economia”, informa o diretor de TI, Gustavo Vieira. Uma das ações foi aumentar em 30% a vida útil dos pneus de caminhões que transportam minério, após a identificação de problemas com uso de sensores. O grupo tem 400 caminhões e cada pneu custa US$ 70 mil. “Só nessa área deixamos de gastar US$ 5 milhões.”
Em três semanas, a Volkswagen vai inaugurar na fábrica do ABC paulista um laboratório de realidade virtual com foco em processos produtivos. Depois terá um para produtos. “Usando equipamentos especiais será possível entrar no projeto virtualmente”, diz Celso Placeres, diretor de Engenharia e Manufatura. Ford e Mercedes-Benz passaram a usar impressoras 3D no desenvolvimento de peças.
Fiat
Prestes a completar 42 anos, a fábrica da Fiat em Betim (MG) avança na corrida para se enquadrar no conceito da indústria 4.0. Entre vários processos adotados, introduziu na linha de montagem exoesqueletos que, acoplados ao corpo do funcionário reduzem o desgaste físico e ajudam a melhorar a produtividade.
Inédita na América Latina, a solução foi introduzida no fim de 2017. Quem exerce funções que podem prejudicar músculos das pernas, braços, ombros e coluna usa a vestimenta robótica que absorve peso e esforço, reduzindo o cansaço.
O exoesqueleto, mais conhecido por seu uso em deficientes físicos, também é utilizado em fábricas da Nissan no Japão e da Audi na Alemanha. A Ford testa seu uso em duas unidades nos Estados Unidos. A Fiat tem 16 conjuntos em Betim e já encomendou mais. Os equipamentos são importados da Suíça e dos EUA e custam US$ 14 mil cada.
“Fiquei mais ágil e menos cansado”, diz Luiz Augusto Barros, de 24 anos, funcionário da Fiat há um ano e meio. Ele trabalha com um exoesqueleto acoplado às costas e às pernas para instalar trancas do capô do Mobi e do Argo, os mais recentes lançamentos da marca. “Antes eu ficava curvado para fazer o serviço, mas agora fico sentado, apoiado pelo exoesqueleto, e só tenho de movimentar os braços.”
Há exoesqueletos dedicados a braços, ombros, coluna e pernas. O fisioterapeuta do trabalho Izonel Farjano explica que foi a solução encontrada para melhorar a condição ergonômica dos operadores naquela fábrica. Segundo ele, a unidade de Pernambuco (da marca Jeep, inaugurada em 2015) já foi concebida com conceitos modernos que evitam esse problema.
Outra iniciativa é a introdução de robôs colaborativos que atuam com os operários, diferentemente dos outros 1,1 mil que ficam cercados por grades por questão de segurança. Um deles entrega peças em uma bandeja para que o funcionário da área de motores não tenha de parar a atividade para pegá-las. Outro faz diversas operações, como aplicar solvente ao redor do para-brisa. “São robôs totalmente seguros e qualquer contato de uma pessoa faz ele parar de imediato”, diz Marcelo Lima, coordenador de Manufatura.
O presidente da Fiat Chrysler Automotive (FCA), Stefan Ketter, afirma já ter constatado ganhos significativos de eficiência, com melhora da produtividade e redução de custos. “O nível de imprevistos e de distúrbios na produção diminuiu muito. Mas este é um processo contínuo e os ganhos de eficiência e qualidade também serão contínuos e crescentes.”
A fábrica também ganhou sala de realidade virtual, onde é possível prever todo o processo produtivo antes da linha ser instalada. O primeiro projeto foi para a montagem do Argo, lançado em maio. “Foi investido R$ 1 milhão na criação da sala e em oito meses já deixamos de gastar R$ 1,3 milhão para corrigir problemas que só seriam identificados quando a produção começasse”, relata o engenheiro Fábio Pugliese.
Em outubro, a empresa inaugurou o Centro de Simulação de Dinâmica Veicular em parceria com a PUC Minas, que cedeu uma sala no câmpus. O sistema, o primeiro da FCA no mundo, tem uma plataforma onde o motorista pode simular todos os movimentos do veículo.
“É possível avaliar as interações do carro com o condutor e com o ambiente, como situações de visibilidade na chuva, no trânsito e interação com pedestres”, informa Toshizaemom Noce, supervisão de Inovação. Um teste recente identificou quanto tempo o condutor deixa de olhar para a estrada quando atende o celular e o que pode ocorrer nesse período. As informações são do jornal O Estado de S. Paulo.
Comentários
Conteúdo para assinantes. Assine JP Premium.